Strakes for the eel drifter
The strakes for the eel drifter are made of oak. However, it was also normal to use pine or larch.
Click on the photos to enlarge them...
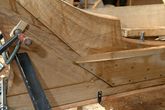
The first strake in the aft is in place
The strakes must fit so well together, that they can be watertight without the use of glue or rubber. They are riveted together with copper nails.
On the old eel drifters, place was made to allow a thin cotton thread to be beaten into the space between the planks, from the outside. We also chose to do this, so that the boat would always be tight, even after a winter on land where the hull had dried out.
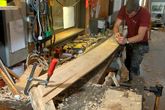
The plank is planed by hand to remove the marks from the thickness planer. The the section where the planks will overlap is planed and prepared to take the next strake.